By Lee Burgess, Interplex
The healthcare sector places several precise demands onto interconnects. The following article will look at the considerations influencing their design and development in order to maximize their suitability in this context. This will particularly focus on what the considerations are going to be from a human perspective – both with regard to the medical professionals using them, and the patients that are receiving treatment.
Interconnection is an essential aspect of modern medical systems. Through the interconnects employed, data and power can be supplied. For example, they may be used to transfer measurements taken by a probe/sensor back to a piece of analyzing equipment. They might also be utilized for delivering current to portable monitoring devices.
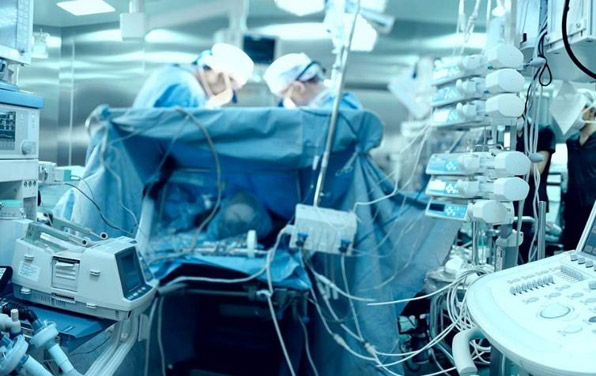
Figure 1: Operating rooms represent extremely challenging environments for medical interconnects
Application considerations
Healthcare undoubtedly presents high-pressure scenarios, where being able to act quickly could make all the difference, resulting in lives being saved. Anything that could cause even split-second indecisiveness or lead to mistakes being made must be avoided. For this reason, how interconnects are handled is of paramount importance – and their external form needs to reflect that.
Having a shape for which the orientation feels intuitive when picked up by the user is certain to be advantageous. It will allow them to plug the interconnect into the associated equipment quicker and without mating errors that could otherwise damage the contacts. This will not only mean that nurses and doctors are more effective in their work, but also ensure that interconnects last longer (with the outlay of having to replace them being lowered). Inclusion of a haptic element that the user will be able to feel will provide further guidance – as in these pressurized settings, operatives will often need to attach cables without having time to look at what they are doing.
Having a shape for which the orientation feels intuitive when picked up by the user is certain to be advantageous. It will allow them to plug the interconnect into the associated equipment quicker and without mating errors that could otherwise damage the contacts. This will not only mean that nurses and doctors are more effective in their work, but also ensure that interconnects last longer (with the outlay of having to replace them being lowered). Inclusion of a haptic element that the user will be able to feel will provide further guidance – as in these pressurized settings, operatives will often need to attach cables without having time to look at what they are doing.
Interconnect properties
In some medical settings, in particular A&E units and operating rooms, there will be exposure to blood and other substances. Likewise, harsh chemicals may be used in periodic cleaning regimes. Hence, interconnects must be fully protected against the prospect of liquid ingress.
Cabling needs to be able to bend sufficiently, as it will be subject to various torsion forces during the average working day. Items of equipment may be stacked closely against each other or pushed against the side of an ambulance wall. Consequently, cables can end up being bent at acute angles. Unless adequately protected against, then damage could occur that will cause interconnect failure. Also, if bending means that a gap appears between the cable and the connector, then liquid could enter and potentially result in a malfunction too.
Whether it is PVC, silicone or some other material being used, the optimal durometer must be selected. If it is too pliable, then the interconnect will bend too far. Conversely, if it is too stiff, then it will not bend appropriately, and cracks will appear. The material must be durable, but also soft enough not to harm the patient if it is directly in touch with them.
If the design needs to be changed, with larger diameter cabling used that can accommodate a greater number of wires, then adjustments will be necessitated. After carrying out finite element analysis, the durometer of the cabling material or the length of the over mold might need to be altered – so that it is properly aligned with the required functional characteristics. The right balance of stiffness and pliability can once again be found and subsequently applied.
Bend/strain relief
In order to maintain continued operation, having bend and strain relief mechanisms will be crucial to interconnect implementations within medical applications. In some circumstances, back potting may need to be included. This will add to production costs, though, so it will normally just be used when absolutely necessary. In many cases, strain relief will be provided by using a ribbed over molding. The downside of this is that the grooves present in such over molds will leave places on the interconnect surface which are very difficult to keep clean. The build-up of bacteria resulting from this is likely to increase the risk of patient infection.
Cost and logistical attributes
It should also be noted that items of medical equipment are expensive to procure, so they will generally remain in operation for a prolonged period of time (possibly two decades or more). Because of this, even if interconnect solutions feature new functionality or performance enhancements, they still have to be backwards compatible with the legacy connectors that were originally designed for that equipment.
For the manufacturers of medical interconnects, the vast majority of their work has focused on providing custom-built solutions. This regularly proves problematic for medical equipment producers, though, as it means they have to make substantial upfront payments to interconnect suppliers to cover the tooling charges. The volumes required will also need to be enough to justify this investment, otherwise the costs involved will simply be too high. In addition, the custom process can take a long time to complete, with several months elapsing before the units are ready.
A better strategy
What medical equipment OEMs actually want is access to off-the-shelf solutions, which will give them more acceptable unit pricing, alongside greater speed to market. They will also be looking for an upgrade path, where new capabilities can be added while at the same time keeping compatibility.
The Interplex Sureline series has been developed with the needs of medical professionals fully taken into account – so convenient, fast-moving usage can be benefited from. With units readily available from stock, these interconnects offer a cost-effective alternative to expensive long lead-time customized production projects. They feature the company’s patented Sureflex over mold technology, which delivers elevated levels of strain relief while having a smoother outer surface, which avoids the collection of dirt and blood that can cause bacteria build-up on other solutions. IPC/WHMA-A-620 Class II standards are conformed with, meaning the operational ruggedness and ongoing reliability are assured.
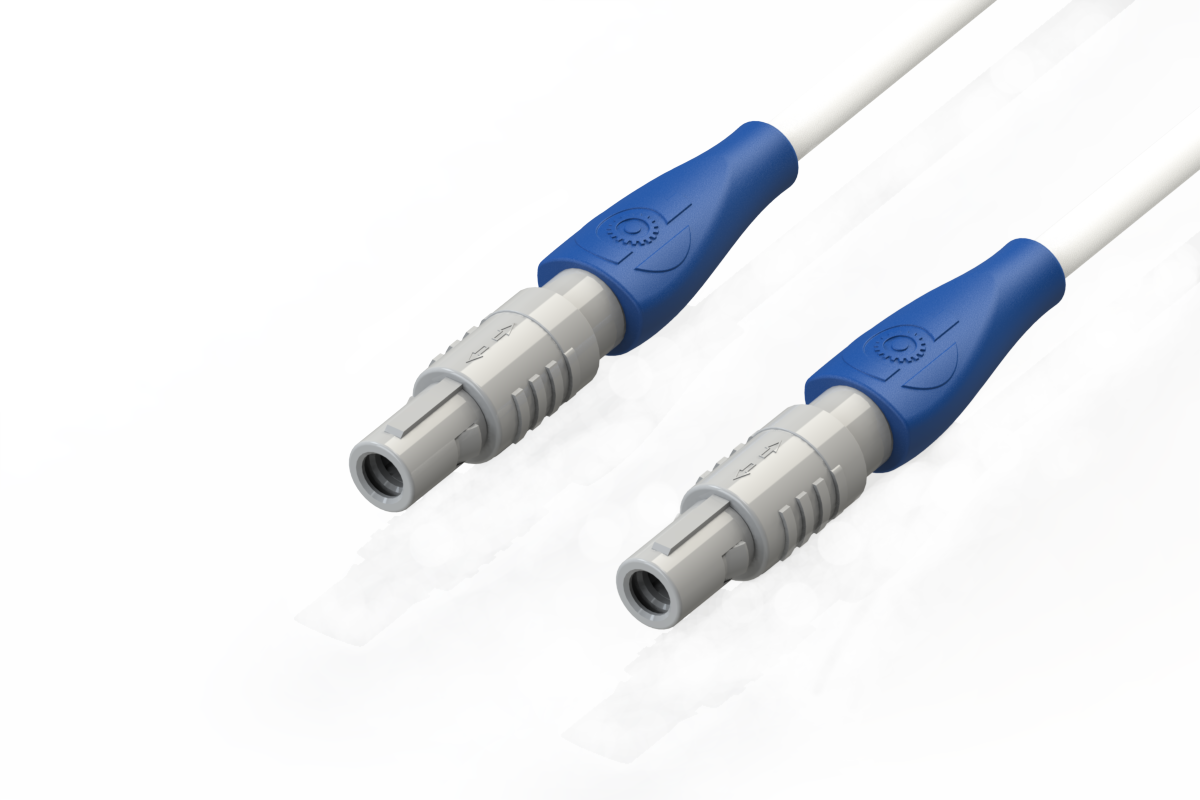
Figure 2: Interplex Sureline interconnect featuring proprietary overmold technology
The circular connector elements used in Sureline products are completely compatible with the REDEL P1 and P2 format that is widely used throughout the healthcare sector. They can be supplied in 14-pole (Plex 1) and 34-pole (Plex 2) versions, with either identical connectors at each end or bare wires at one end. The accompanying cable assemblies can be specified in lengths of 3 feet, 6 feet and 10 feet. Further, cable lengths and pin configurations are scheduled for introduction soon.
How the external shape has been formed makes it natural for users to grip these interconnects in the intended orientation (and it actually feels wrong if they are not held in the correct way). Each has a dimple on the outer surface that gives further guidance about what the right orientation should be. The upshot of all this is that Sureline interconnects will be inserted into the ports of medical equipment correctly during mating – so mating is achieved quicker and the unwanted wear-and-tear that comes with mis-mating attempts is mitigated.
As well as being highly suited to large numbers of mating cycles (with a 1500-cycle durability), these interconnects are also applicable to limited-use situations (where they have to be disposed of after a relatively short period of time). They have an IP50 rating that safeguards against liquid ingress and are autoclave sterilizable too. Operational temperatures up to 150 °C are supported as standard, but versions intended for operation reaching 170 °C are also available.
By using the Sureline interconnect platform, another benefit for medical equipment OEMs is that the product validation process is made much more straightforward. After one product has been validated, then this validation will be applicable to other products too.
Conclusion
Utilizing interconnects that have ergonomic designs will facilitate quicker operation and accelerate the responsiveness of medical staff in critical scenarios where patients’ lives may be in danger. Off-the-shelf solutions will minimize the investment that equipment OEMs need to make and enable them to complete their development projects within shorter timeframes. Innovative engineering can also protect against functionality being compromised and lower the TCO for purchasing departments. Finally, the ability to upgrade interconnect technology, so that retrofitting onto existing equipment assets is possible, is going to be very appealing too. These expectations are set to alter the way in which medical interconnect supply is approached.